
QUALITY

Manufacturing Process
for conveyor rollers
We have fully automated standalone machinery which are SPM for idler manufacturing which is automatic pipe cutting machine, double headed boring machine, double headed automatic welding machine, automatic assembly machine, polygon turning machine and CNC turning machine, PLC based automatic cutting for shaft. We have a production capacity of more than 400 idlers per day.
​
In our production line Pipe Process and Shaft process both are done parallel. So, in production line takes less time in processing on machinery.
Part - 1 (PIPE PROCESS)
Step 1 - PIPE CUTTING
(AUTOMATIC PIPE CUTTING & BEVELING MACHINE)
In this first Operator feeds the machine with tubes by crane or manual. Total load volume of loading & storage rack is 19 pieces of φ159 tubes with 4 tons’ load capacity. The storage rack is designed with a proper incline angle to enable the tube roll downward to kick-in position. The kick-in plates are driven by multiple-units of air cylinder, which can kick the tube onto feeding roller table one after another.
In this the pipe length fixing is done by AC servo system. So, feeding the tube with precise length.All cut piece of pipe will be equally in length with help of parting & bevelling tool.
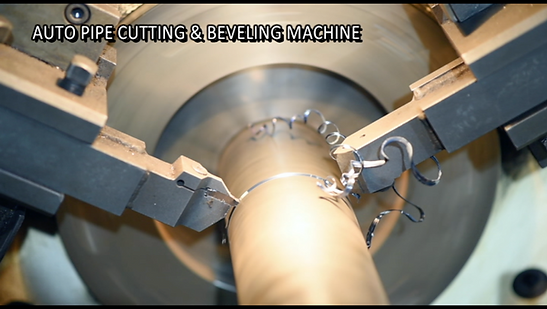

Step 2 - PIPE BORING
(AUTOMATIC DOUBLE HEADED PIPE BORING)
In this machine align clamping mechanism installed. Which are driven by electric motor. So, that we can controlled the boring depth with high accuracy. Dimensional tolerance between both bore space ≤ 0.20. Pipes will be bored simultaneously both side to avoid concentricity.
Step 3 - CO2 MIG WELDING
(AUTOMATIC DOUBLE HEADED CO2 MIG WELDING)
This machine is designed such like that the nozzle cleaning and wire shearing function done easily. So, the welding component production capacity is increased with good quality compared to manual process.

Part - 2 (SHAFT PROCESS)
Step 1 - SHAFT CUTTING
(AUTOMATIC SHAFT CUTTING WITH PLC PROGRAMING)
In this process cutting machine consists of a part called bi-metal blade is used to cut the metal. This cutter blade held such a like that blade is rotated and fed into the work at variable speeds. And in this we used PLC based automatic system for performing this task. So, we can get the higher production capacity with good quality work.


Step 2 - SHAFT MILLING
(CNC SHAFT MILLING WITH SYNCHRONISE ARRANGEMENT)
We are performing this operation on the polygon turning machine. And it takes the shortest cutting time compared to conventional milling machine. So, we achieved high productivity with precise work in short time.
Step 3 - SHAFT GROOVING
(CNC TURNING CENTRE)
This task performs on the CNC Turning machine. In which we get high precision work within less time-consuming period due to precise machine availability. In this we get the accuracy in the operation up to 0.007mm.

Part - 3 (ASSEMBLY)
Step 1 - AUTOMATIC DOUBLE HEAD BEARING AND SEALING ASSEMBLY
This machine is used for assembling bearing/seal/dust cap into the roller. The bearing/seal/dust cap shall be loaded onto the pressing head by manual, and pressing head press the bearing/seal/dust cap onto the both end of roller at one time. After bearing and sealing are assembled, the operator shall manually be assembled the keylock. This machine specially designed with buffer pressing structure. We ensure you about assembling precision as well as avoiding the defects like inadequate assembling and distortion etc.

Part - 4 (Testing & Inspection)
1) Total indicated runout(TIR)
As per IS 8598 maximum allowable run out is 1.6mm. and for that we measuring the run out of roller with the help of Dial indicator. And our guaranteed run out is not more than 1mm due to our highly-automated quality machinery and manufacturing process.
2) Axial Float
Axial float (End play) is the important parameter for the roller. And for that we are grooving the shaft on the CNC Turning machine which is highly precise. So, we get the accuracy up to 0.007mm. and which is very negligible.
3) Water ingredient test
The water proof shall be carried out in a chamber where an idler Shall be placed on a bracket and subjected to a test: run at more than the actual working Speed encountered at site. Water at a pressure of 1-2kg/cm. shall be impinging on roller On both sides of bearing housing. Each roller shall be tested under water for 10-20 minutes. After the test the idler roller shall be dismantled and bearing be checked for water contamination. There should not be any droplets/moisture observed inside the bearing area and the grease color should not change in such a way which is attributed to the water contamination. The test shall be conducted in the presence of customer or TPI representative and shall be done at random at a ratio of 2:500 quantam.
4) Dust ingredient test
The dust proof test shall be carried out in a chamber where an idler shall be placed on a bracket and subjected to a test run at more than the actual working speed encountered at site. The dust shall be agitated and blown continuously for 10-20 minutes. After the test the idler roller shall be dismantled and bearing be checked for any dust. There should not be any dust inside bearing area and grease colour should not be changed. Should be with in 5% permissible. The test shall be conducted in the presence of customer representative and shall be done at random at a ratio of 2:500.
5) Friction factor test
dlers will be rotated (100-125) % of normal RPM. The speed will be checked by a calculation available with CONVERO as per machine designed rpm. All of a sudden rotating source will be removed and the stop watch put into operation. Due to friction, the idler slowly come to rest. The period of dying down will be measured in the stop watch.
Friction factor[F]: 0.02 Maximum.
6) Roller resistance test/Drag test
Idlers will be rotated at normal RPM. RoIdler will be mount on pipe surface and shaft will be free to move without any disturbance. A locking nut will be placed at shaft end and a pin will be placed on scale. The measured scale should be noted for 5-10 secs. Due to load on shaft and locking nut, scale will show drag force required to rotate roller.
Resistance/Drag.[RDt]: 459 gram Maximum.
​

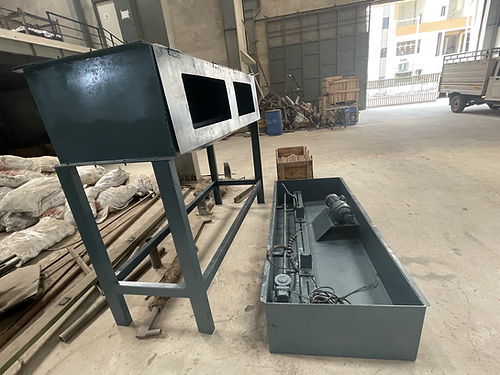

Part - 5 (Painting & Packing)
Cleaning with special chemical for better bonding of paint.
All products are painted precisely with EPOXY/PU paint as per end client requirement
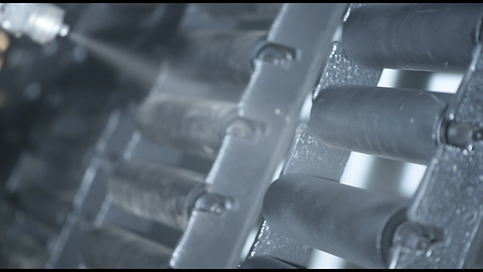
Design & Production
Self-design seal set filled with hi-lithium grease.
Self-made housing with machining as per required tolerance for better fitment.
Strength
OEM vendor of SKF INDIA LTD
ERP Based Documentation